I. 서 론
최근 3D 프린팅 기술은 물류 선박 제조, 우주용 소형 부품 생산, 로켓 발사체 제작 외 생명공학, 식품, 자동차, 항공, 우주, 방위 산업에서 다방면으로 활용되고 있다[1]. 3D 프린팅 기술의 강점은 제작 시간, 재료 소모성, 소모 에너지 측면에서의 높은 경제성과 높은 설계 자유도이다[2]. 아울러, 다품목 소량 생산에 적합한 제조 기술로 연구개발 시제품 생산에 활용성이 높다. 이러한 강점을 활용하여 적층 제조 기술은 민수, 국방 분야의 차세대 밀리미터파 부품 개발에 적극적으로 활용되고 있다.
밀리미터파 부품은 6G 통신, 차세대 레이다, 위성 통신, 원격 정밀 감지, 고해상도 이미지 센서 등에 적용될 수 있어 부품 개발의 중요성이 강조됨에 따라[1],[3] 국내에서는 적층 제조 기술을 활용하여 Ku·Ka 대역(Ku: 12~18 GHz, Ka: 26.5~40 GHz) Helical 안테나, 개구면 배열 안테나 등의 밀리미터파 부품을 연구개발하고 있다[4]. 국외에서는 중국, 일본, 미국 등을 중심으로 안테나 외 다양한 형태의 도파관 제작에도 활용되고 있는데[5]~[7], 일반 제조 기술로 제작할 수 있었던 형태에 국한되지 않고, 내부에 기하학적 형상이 포함된 혁신적인 설계를 시도 및 제작하고 있다.
밀리미터파 활용 분야가 구체화 되고 적층 제조를 포함한 제작 기술의 고도화 덕분에 밀리미터파 RF 신호원과 증폭기의 개발 요구 성능도 다양화됐다. 그 중, 주파수가 올라감에도 상대적으로 작고, 효율이 높으며, 높은 RF 전력(power)을 요구하는 분야에서 진행파관 증폭기(traveling wave tube amplifier)가 재 주목받고 있다[8]~[10]. 밀리미터파 진행파관 증폭기는 군사적으로도 활용 가치가 있어, 국내 전자기 스펙트럼 기술 확보와 적층 제조 기술의 진행파관 증폭기 부품 제작 활용 가능성을 확인하기 위해 중요 구성품인 저속파 구조 도파관(slow-wave structure waveguide)을 설계하고 제작하였다. 활용 가능성 판단은 정밀 절삭 가공으로 제작한 동일 제작품과 비교하여 기술하였다.
II. 저속파 구조 도파관 및 적층 제조
금속 적층 제조 기술로 제작한 저속파 구조 도파관은 W 대역(75~110 GHz)에서 전자빔과 상호 작용을 통해 입력된 RF 신호를 증폭하는 역할을 한다. 구조 설계는 참문헌 [11]을 참고했다. 저속파 구조 도파관이 고온 환경에 노출되는 점, 진공 상태에서 쓰일 것을 고려하여 내열성과 고온에서의 열변형 및 out-gasing이 염려되는 레진 등의 폴리머 프린팅 후 electroless plating이나 금속 코팅[12]하는 방법은 시도하지 않았다.
제작 3D 모델 구조와 주요 치수는 그림 1에 나타냈다. 전체 크기는 35×2×68.56 mm이며 내부 구조 중 가장 구현이 힘들 것으로 예상되는 곳의 치수는 약 0.2 mm이다. 내부 채널에는 RF 신호가 전송되며, 빨간색으로 표시된 사각형 부분은 WR10 standard 형상으로 75~110 GHz 대역에 쓰는 표준 도파관(치수: 2.54×1.27 mm)이다. 전달률 및 반사율 측정을 위해서 도파관에 정렬 핀과 나사산 구멍 구조를 반영하였으며, 이 부분은 후가공으로 제작하였다. 그림 1처럼 제작할 도파관은 단순한 직선 도파관이 아니라 구불구불한 구조이기 때문에 프린팅 완료 후 분말 제거가 힘들고, 그림 1의 a/b 비율도 7 정도로 제작 형상이 변형될 가능성이 있어 제작 난이도 측면에서도 매우 까다롭다. 전자빔이 지나는 원형 터널의 직경 ‘t’는 0.42 mm로 매우 작은 편이라 정확한 원형 구현 여부가 중요하다.
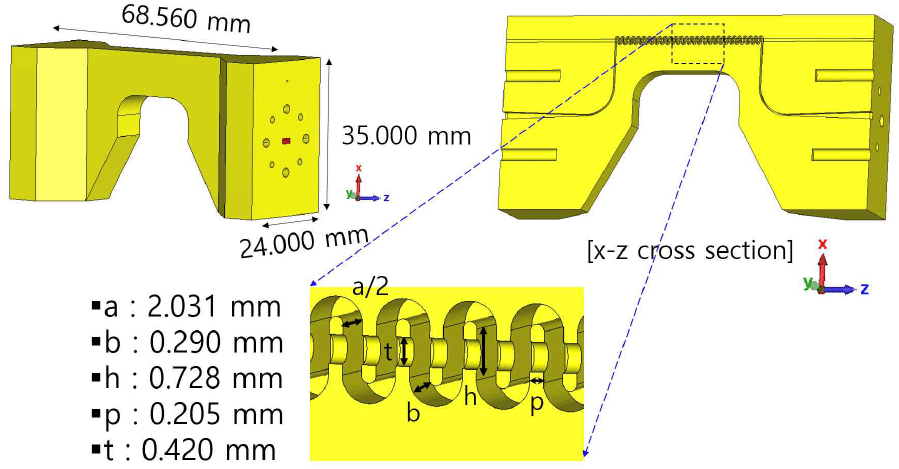
그림 1의 구조를 CL80CU Bronze, AlSi10Mg, CuCP의 3개 소재로 제작하였다. 3D 프린터 정보는 부록에 기재하였다. 금속 파우더 재사용 시, 전기전도도의 저하로 이어지므로 한 번도 사용하지 않은 초기 분말을 사용했다. CL80CU의 전기전도도는 International Annealed Copper Standard(IACS, σ=5.8×107 S/m) 기준 15 %이며, 금속 분말의 평균 입도는 20~40 μm이다. GE 사의 Mlab100를 사용하여 적층하였고, 적층 두께는 15 μm로 제작하였다. AlSi10Mg의 전기 전도성은 IACS 기준 44 %로 EOS에서 가장 높은 소재이다. 평균 분말의 입도는 25~70 μm이며, EOS GmbH 社의 M290-1kW 장비로 제작하였다. 적층 두께는 30 μm로 제작했다. 마지막으로 사용한 소재는 CuCP 이며 전기 전도성은 IACS 기준 100.7 %이다. CuCP 재료의 평균 분말의 입도는 15~53 μm이며 적층 두께는 40 μm로 제작했다. 제작 후 후처리는 분말 제거, 열 해소를 위한 stress relief(최대 온도: 190°C, 2시간, Ar 분위기)만 실시했다. 화학연마로 인한 내부 채널 손상은 RF 통과 대역과 반사 대역의 결과 분석에 영향을 줄 수 있어, 이소프로필 알코올을 이용한 초음파 세정만 진행하였다.
III. 제작 결과 및 분석
본 장은 적층 제조를 통해 다수 제작한 것과 정밀 절삭 1회 가공품을 검사한 비교 결과를 제시한다. 제작된 저속파 구조 도파관은 비파괴 검사, 파괴 후 현미경 검사, 그리고 벡터 회로망 분석기를 통한 RF 투과율/반사율 측정으로 분석하였다. 그리고 측정된 조도를 기반으로 전기전도도를 예측해보고 실험값과 비교해보았다.
그림 2는 적층 제조된 저속파 구조 도파관이다. 그림 2(a)의 외형이 타 제작품과 다소 다르지만, 내부 구조는 동일하다. 그림 3은 Bronze로 적층 제조한 제품의 비파괴 검사 CT scan 결과이다. CT scan을 통해 절단하지 않더라도 내부 분말 확인, 기공 검출, 치수 측정 확인을 할 수 있을 것이라 기대했으나, CT 투영 촬영 특성상 비중, 밀도에 따른 왜곡, 난반사 문제로 정확한 치수 측정은 어려웠다. 그럼에도 그림 1의 ‘t’의 터널 구조는 그림 3(a)에서 막힌 곳 없이 제작된 것이 확인되었으며, 그림 3(b)처럼 도파관 내 잔여 분말은 검출되지 않았다. 그러나 파괴 검사 시, 도파관 내부에서 잔여 분말이 확인되었다.
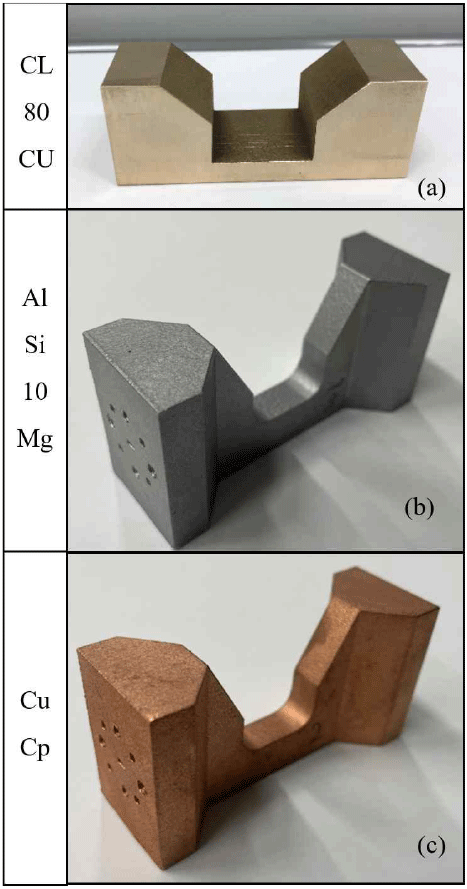
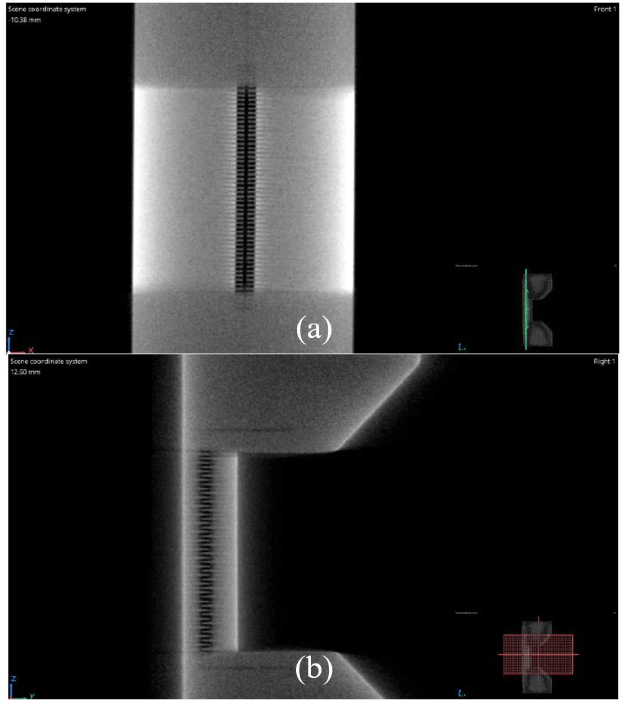
다음은 광학 현미경을 이용하여 외부 구조의 치수와 절단된 도파관 내부의 치수를 측정하여 그림 4과 5에 나타냈다. 그림 4(a)에 표시한 부분을 확대하여 측정한 결과 그림 1의 ‘t’ 치수는 그림 4(b) 및 그림 4(d)에서 확인할 수 있듯이 각각 0.398 mm, 0.585 mm로 나왔다. AlSi10Mg의 경우 외부에 터널 형태가 보이지만 내부는 부분적으로 막혀 있어, 터널 구조가 막히지 않은 CL80CU 적층 결과만 고려하면 최소 제작 오차는 22 μm로 준수한다. 반면에, 그림 4(f)에서는 터널 구조를 찾아볼 수 없다. 그림 4(c), 그림 4(e) 및 그림 4 (g)의 WR10 도파관 부분을 측정한 결과는 표 1 에 정리하였다.
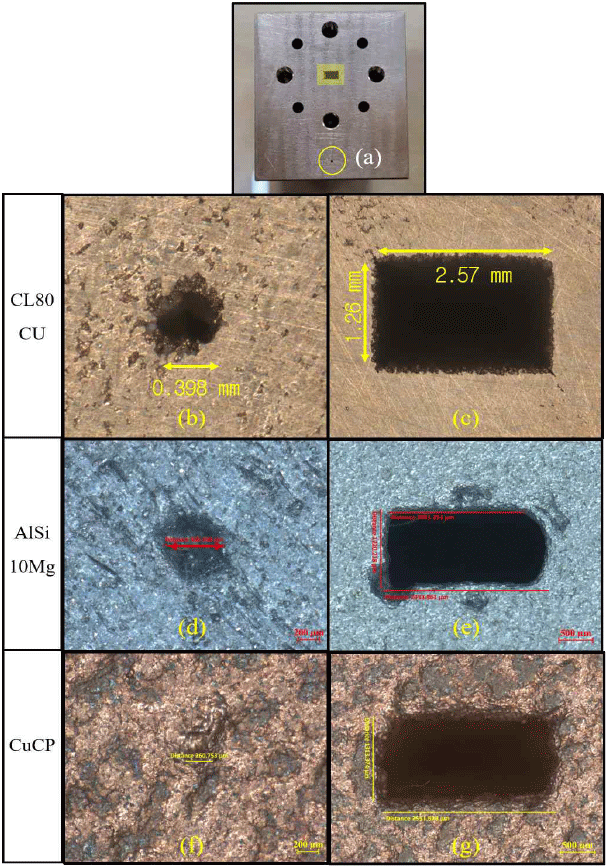
측정 결과 AlSi10Mg의 제작 오차가 최대 176 μm로 가장 컸으며 CL80CU의 오차는 30 μm로 일반 가공 수준 정도로 정밀했다. 내부 구조를 측정하기 위해 저속파 구조 도파관을 절단하였고 측정한 결과를 그림 5에 나타냈다. 그림 5(b) 및 그림 5(c)에서 그림 1의 ‘t’ 구조가 제대로 구현되지 않았고, 그림 5(c)의 경우는 그림 1의 ‘p’ 구조도 적층 되지 않았다. 그림 5(a)만 저속파 구조가 제대로 적층 되어, 측정 결과를 표 2에 정리하였다. 표 2의 측정 결과 수치는 평균값이며 구조 변수별 최대 제작 오차는 95 μm로 측정됐다. 저속파 구조 도파관은 제작 정밀도가 중요하지만 동시에 RF 신호가 전달되므로 전달 손실과 연관된 표면 조도도 매우 중요하여 재료별로 평가해보았다.
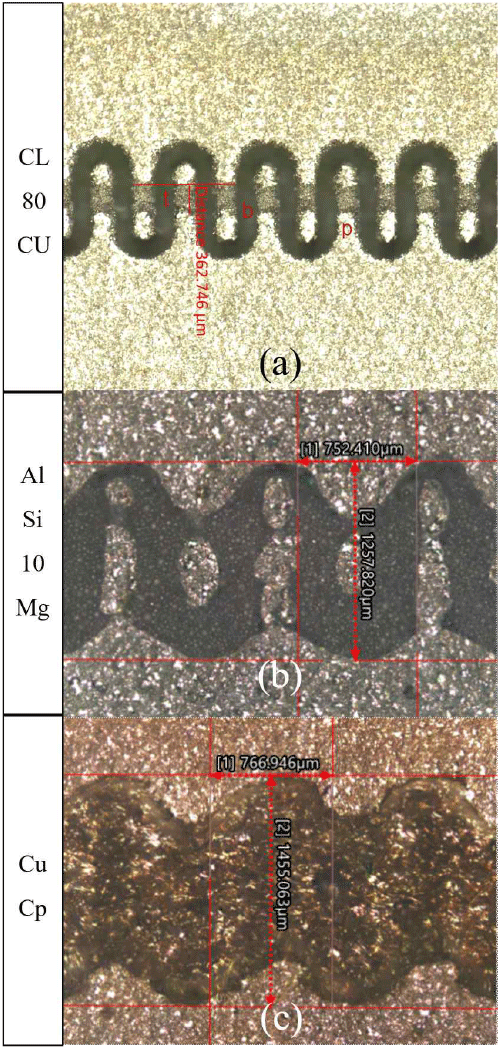
Measured dimensions | Avg. value (mm) | Avg. error (mm) |
---|---|---|
p | 0.269 | 0.064 |
t | 0.365 | −0.055 |
b | 0.248 | −0.042 |
적층 제조된 도파관의 표면 조도를 측정하여 표 3에 결과를 정리하였다. 측정은 나노시스템의 NV-3000 3차원 비접촉식 측정기를 활용하였다. 각 샘플에서도 위치를 변경해가며 데이터를 얻어 평균값을 산출하였다. CuCP를 제외하고, 평균 분말의 입도 대비 31~50 % 사이의 값을 얻었으며 CuCP의 표면 조도는 입도 대비 53~68 %로 비교적 크다. 표 3에 조도 측정 결과와 식 (1)을 활용한 유효 전기전도도(σeff) 예측값을 나타냈다[13].
Materials | Avg. value (μm) | σeff/IACS (%) |
---|---|---|
CL80CU | 15.08 | 3.75 |
AlSi10Mg | 29.35 | 11.00 |
CuCP | 36.01 | 25.00 |
식 (1)에서 유효 전기전도도는 표면 깊이(δ, skin depth)와 RMS 표면조도(△)의 영향을 받는다. 표 3의 유효 전기전도도는 주파수 범위를 80~90 GHz로 제한했을 때 얻어진 값이며, 재료 고유의 전기전도도(σD)를 제외하고 표면 조도로 인한 유효 전기전도도 감소는 75 %이다.
적층 제조된 저속파 구조 도파관과 1:1 비교를 위해 나노 가공기를 이용해 전통적인 절삭 방법으로 동일 구조를 무산소동(OFC, oxygen free copper)에 제작하였다. 제작 결과, 그림 6과 같이 평균 오차는 6 μm 이내이며, 절삭 가공으로 인한 버(Burr)와 표면의 절삭유 흔적이 보인다.
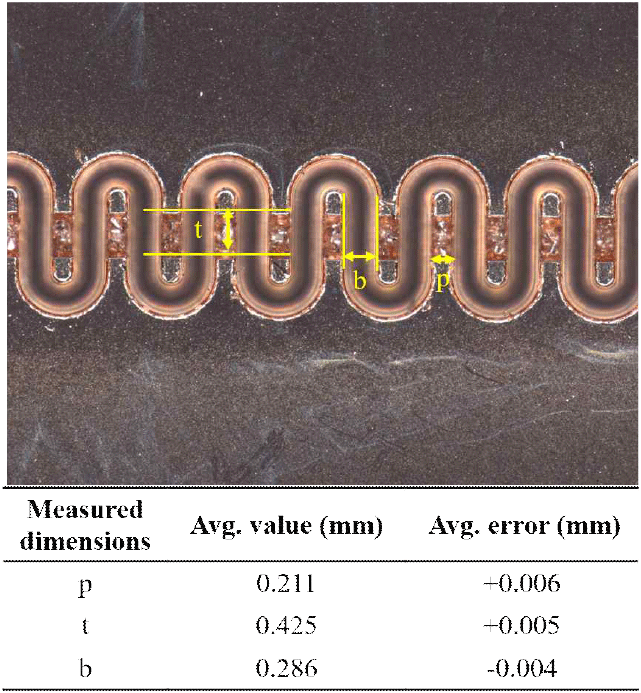
측정된 표면 조도는 50 nm 정도이며, 동일 조건에서 유효 전기전도도는 5.534×107 S/m 로 IACS 대비 5 % 감소로 계산되었다.
저속파 구조 도파관은 궁극적으로 RF 신호를 전달해야 하므로 RF 전달 특성이 가장 중요하다. 적층 제작된 저속파 구조 도파관은 AlSi10Mg와 CuCP의 경우 내부 구조 구현이 완벽하지 않았으므로 CL80CU 제작품만 벡터 회로망 분석기로 RF 전달 특성을 측정하였다. 대신, AlSi10Mg와 CuCP는 2인치 길이의 직선 도파관을 추가 제작하여 RF 전달 특성을 측정하고 예측된 유효 전기전도도와 비교해보았다.
그림 7(a)는 두 제작품의 S11 및 S21 측정 결과와 전산모사 결과를 나타낸다. CL80CU 제작품의 경우, S11 그래프에서 2 GHz 정도의 차단 주파수 편이가 확인되며, 80 GHz 이상 영역에서 시뮬레이션 대비 반사 레벨이 평균 8 dB 크다. S21의 경우, 시뮬레이션 대비 34 dB 크다. 제작 오차가 크지 않았음에도 유효 전기전도도로 계산된 전달 손실과 측정된 전달 손실에서 큰 차이를 보이는 것은 파괴 검사에서 도파관 양 끝의 잔여 파우더로 인해 주파수 통과 대역에 영향은 적었으나 표면 손실의 증가가 원인으로 판단된다. OFC에 절삭 가공한 경우, 0.5 GHz의 차단 주파수 편이가 보이며 측정값과 가장 유사하도록 전산모사 내 설정한 전기전도도와 표면 조도 정보로 예측된 유효전기전도도의 차이가 0.5 %로 높은 일치율을 보였다. 그림 7(b)는 AlSi10Mg와 CuCP 재료로 직선 도파관을 추가 제작하여 측정한 값과 유효 전기전도도로 전산 모사한 값을 비교한 그래프이다. AlSi10Mg 직선 도파관의 경우 반사 신호가 −15 dB로 다소 높고, 전달 신호는 측정값이 전산모사 값 대비 약 0.3 dB 낮다. 높은 반사 신호로 인해 S11 및 S21 측정값을 기반으로 AlSi10Mg의 전기전도도를 추산한 값(≈2.65×106 S/m)과 비교 시, 계산된 유효 전기전도도와 59% 차이를 보인다. CuCP의 경우 삽입 손실이 커 식 (1)로 계산된 유효 전기전도도와 비교가 어렵다. 유독 CuCP로 적층 제조된 도파관의 반사 신호가 컸던 원인을 분석해보았다.
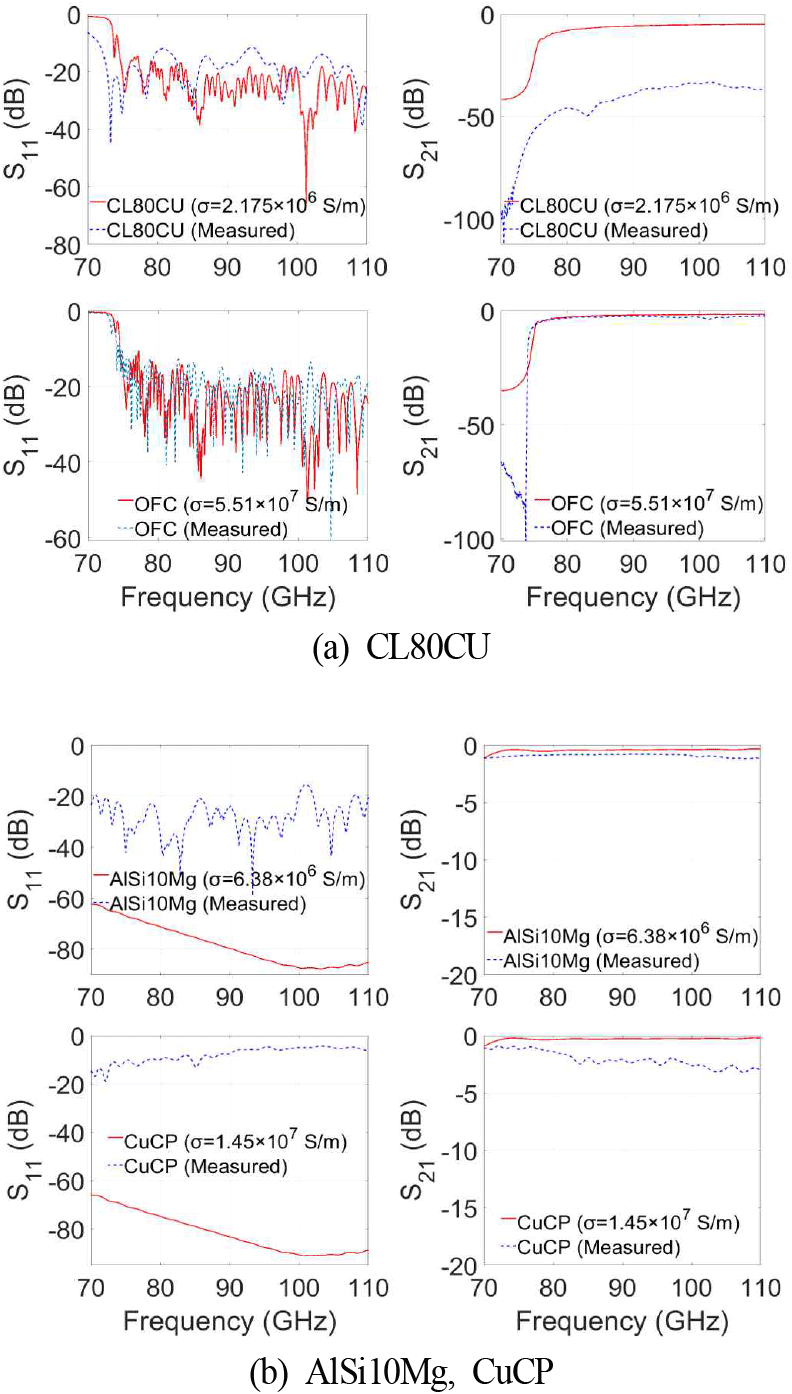
그림 8은 AlSi10Mg와 CuCP의 직선 도파관의 S11 및 S21 측정과 전산모사 비교 결과를 보여준다. 그림 8의 현미경 사진을 보면 제작품 내부 모습에서 볼 수 있듯이 CuCP의 경우, AlSi10Mg 대비 노란색 점선으로 나타낸 부분에서 원인 미상의 소결체가 관찰되었으며, 이 외에도 크기는 작지만 직선 도파관 내 유사한 구조가 확인되었다. AlSi10Mg의 경우 CuCP 만큼의 큰 소결 구조는 관찰되지는 않으나, 내부 표면에 작은 요철 구조가 확인되었다. 이와 같은 소결 구조체와 불균일한 표면이 RF 전달 특성에 미치는 영향을 분석하기 위해 도파관 개구 크기는 측정된 치수 결과를 반영하였고, 균일하지 않은 표면과 소결체를 유사한 크기의 단순 블록 형상으로 모사하여 시뮬레이션을 수행하였다. 그림 8의 S11과 S21처럼 전산 모사 결과와 측정 결과가 유사한 경향을 보임을 확인하였고, 예측하지 못한 구조들의 다중효과로 인해 전기적 특성에 영향을 미치고 있음을 확인하였다.
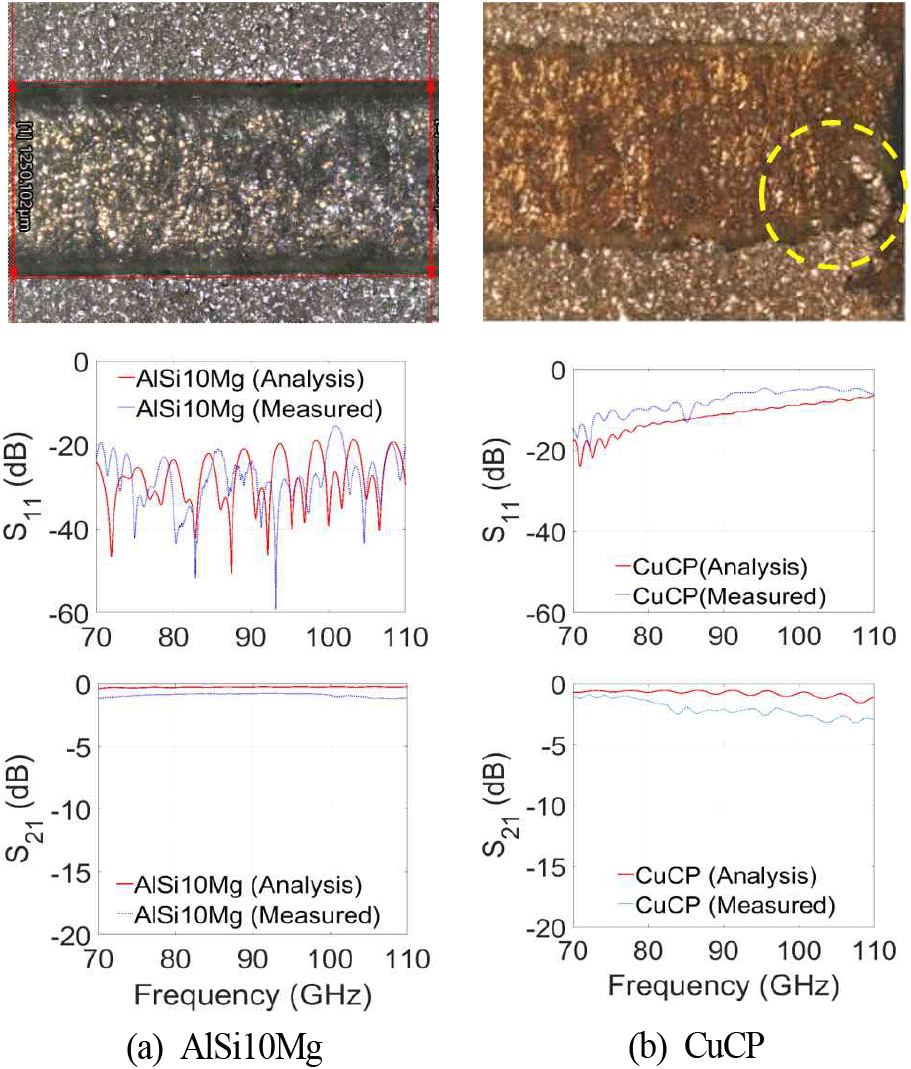
IV. 결 론
본 논문에서 우리는 다양한 무기체계에 활용되고 있는 고출력 RF 증폭기 중 한 부속품인 저속파 구조 도파관을 적층 제조 기술로 3가지 재료를 이용해 제작하고 평가한 내용을 다루었다. 80 GHz 이상 영역에서 동작하는 도파관 제작에 적층 제조 기술 활용 시, 재료, 최소 치수(0.2 mm), 구조에 따라 구현성 차이가 확연하였다. CuCP 소재는 동일 구조를 제작하더라도 재현성 차이가 있었으며 직경 0.42 mm의 구멍과 최소 치수 0.2 mm의 구조는 구현하지 못한다. AlSi10Mg의 경우 소결 범위를 더 줄일 수 있다면 해당 구멍과 최소 구조 구현 가능성이 높아 보인다. 적층 제조 시, 재료마다 다른 제작 조건과 평균 입도로 소결되었으나 표면 조도로 인한 전기전도도 손실은 75 %로 거의 동일했으며, 별도의 화학연마 후처리가 없다면 표면 조도는 평균 입도의 50 %로 간주하여 유효전기전도도를 예측해도 무방하다. 다만, 예측 전기전도도를 RF 투과 실험로 검증하기 위해서는 반사 신호가 유사해야 한다. CL80CU 경우처럼 잘 제작되더라도 금속 파우더 제거가 완벽하지 않으면 상당한 전달 손실이 발생함을 확인하였다. 아울러, 3-3장에서 적층 제조의 제작 오차와 소결 가운데 발생하는 예측 불가능한 구조로 RF 특성 변화가 더 컸다는 점은 화학연마 또는 파우더의 평균 입도를 1 μm 이하로 만들어 RF 신호의 손실을 줄이는 것보다 제작 가능 최소 치수, 제작 정밀도와 재현성 개선이 우선 과제임을 보여준다. 결론적으로 절삭 가공된 것과 비교했을 때, 제작 시간 및 비용 제외 모든 면에서 경쟁력이 낮지만, CL80CU와 AlSi10Mg 소재는 소결 범위 최소화와 후처리 연구를 통해 W 대역 저속파 구조 도파관 제작에 활용 가능성이 있으며, 더 미세한 금속 분말 재료 개발이 가능하다면 RF 부품 제작의 활용성이 가속화되리라 판단된다. 그러나, 높은 전기전도도로 RF 부품 제작에 가장 매력적인 CuCP 소재는 W 대역 RF 부품 제작에 활용하기 시기상조로 판단된다.
부 록
CL80CU의 재료로 저속파 구조 도파관을 프린팅할 때 활용한 장비는 GE 사의 Mlab100이며, AlSi10Mg와 CuCP로 동일 구조를 프린팅할 때는 EOS 사의 M290 장비로 제작하였다. 기본적인 성능 정보는 표 4에 나타냈다.